Intelligent, Rapid, and Optimized Dimensional Inspection (IRODI)
Revolutionizing Manufacturing Efficiency and Accuracy with New In-Process and Post-Process Inspection Methods
technology Snapshot
Overview
Manufacturers rely on precise dimensional inspections to meet engineering specifications; however, traditional methods are slow, create bottlenecks, and often rely on offsite measurements. The IRODI system is being developed to address these challenges by enabling realtime, in-process inspections on the production floor through the integration of optical scanning and the accuracy of coordinate measuring machines (CMMs).
A key component of IRODI, the Maestro software, has been tested in a lab setting using CMMs and laser scanners to perform dimensional inspections of machined components. Maestro integrates with existing metrology tools to coordinate inspections, analyze measurement data, and optimize quality control.
The full IRODI system is designed to automate inspection planning, enable on-machine inspection across both subtractive and additive processes, identify defects earlier, reduce rework, support real-time decisionmaking, and integrate seamlessly with current manufacturing environments.
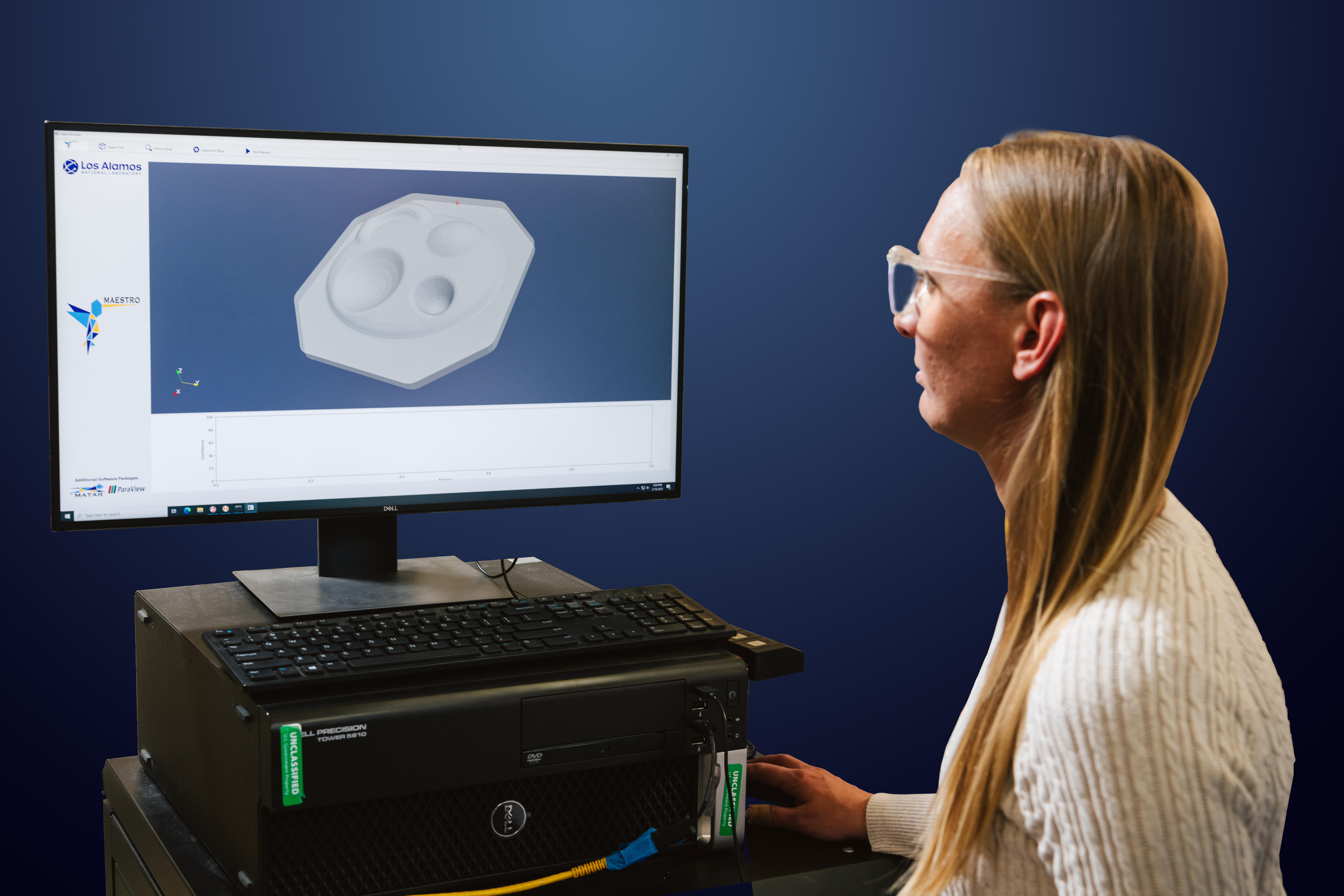
Advantages
- Real-Time & Virtual Inspections: Enables dimensional validation both during manufacturing and in the design phase through virtual simulations, ensuring parts are optimized for inspection needs before production begins.
- Waste Reduction: Identifies defects early, minimizing material waste, production inefficiencies, and costly redesigns.
- Optimized Assembly Fit: Matches mating parts with compatible tolerances for better performance, reducing rework and misalignment issues.
- Seamless Integration: Works with existing inspection tools and design software, ensuring alignment between manufacturing hardware and quality control processes.
- Scalable & Flexible: Supports both small-scale and large-scale manufacturing operations, adapting to various production environments.
Technology Description
The IRODI system integrates advanced inspection hardware with intelligent algorithms powered by its Maestro software, which serves as the core platform for coordinating dimensional inspection and data analysis.
Key features include:
- Embedded Intelligence: Adaptive algorithms identify critical measurement points, balancing speed and accuracy.
- Real-Time Measurements: Provides immediate dimensional feedback during manufacturing to eliminate bottlenecks.
- Component Pairing: Intelligently matches parts for optimal fit based on tolerance analysis.
- Tool Compatibility: Designed to work seamlessly with CMMs, CNC systems, laser scanners, and other metrology equipment.
Market Applications
IRODI is designed for industries that require high-precision, efficient, and scalable dimensional inspection solutions:
- Advanced Manufacturing: Enhances inspection processes for both additive (3D printing) and subtractive (CNC machining) methods, ensuring part accuracy and consistency.
- Medical Devices: Verifies the precision of implants, surgical instruments, and micro-scale components, where even slight dimensional variations can impact performance.
- Automotive: Ensures dimensional accuracy in engine, transmission, and chassis components, improving assembly fit and reliability.
- Semiconductors: Supports microelectronics manufacturing, though specific metrology tools at this scale (e.g., nanometer vs. micron precision) need further evaluation.
- Nuclear & Energy: Validates components used in reactors, turbines, and high-risk environments to ensure compliance with stringent safety standards.
- Aerospace & Defense: Guarantees that mission-critical components meet exacting tolerances for safety and performance in aircraft, spacecraft, and defense systems.
Next Steps
IRODI is advancing toward full-scale industrial implementation, with ongoing testing and validation. Future development efforts will target commercial markets, beginning with nuclear and national security applications where precision, safety, and traceability are essential. These efforts aim to demonstrate the system’s value in high-stakes environments while meeting stringent performance requirements.
LANL is actively seeking industry partners, particularly manufacturers and metrology system providers, to support the next phase of development. Key objectives include
- integrating IRODI into existing metrology and production environments;
- conducting targeted testing to refine system accuracy, reliability, and scalability; and
- licensing intellectual property and co-developing commercial products for high-precision manufacturing markets.